Steam and hot water boilers are essential heating solutions for various industrial and commercial applications, with specific system requirements based on temperature, pressure, fuel, and load needs.
When purchasing boilers, it is important to evaluate the application, facilities, and system requirements in order to choose the best model for the job. Koch Applied Solutions represents all the different styles and types of boilers, so our team is able to perform an evaluation and make application specific recommendations based on your needs and goals for the project.
Learn more:
Steam & Hot Water Boiler Manufacturers
Koch Applied Solutions works with Superior Boiler for boiler solutions engineered for optimal efficiency, excellent performance, and the utmost reliability.
Superior Boiler is recognized around the globe as a leading manufacturer of boiler systems and equipment for process steam, hot water, and waste heat recovery.
Koch Applied Solutions works with Miura to offer steam boilers designed to meet challenging load requirements with a modular on-demand steam plant.
Miura boilers can meet lower NOx standards, reduce maintenance and monitoring needs, and reduce space requirements. The unique, compact modular Miura boiler design utilizes a low-volume pressure vessel, offering output capacities comparable to much larger traditional, outdated boilers. The resulting smaller boiler footprint provides design flexibility, reduced construction costs and more options with existing spaces.
Precision Boilers is known for providing the performance and reliability that system design engineers and facility owners depend on.
Standard models are designed and fabricated to strict industry standards and are available with a comprehensive accessory package to meet a wide variety of requirements and application needs. Precision offers customized solutions, including more sophisticated control options and special trim components to provide a tailor-made solution.
Koch Applied Solutions partners with Patterson-Kelley to offer a full-line of condensing and non-condensing hot water boilers as well as instantaneous and semi-instantaneous water heaters.
Located in East Stroudsburg, Pennsylvania, Patterson-Kelley is a recognized market leader and major producer of heat transfer equipment. These hot water boilers and water heaters are installed in institutional, commercial, and industrial building applications in a variety of markets.
Unilux steam and hot water boilers are the first 5-pass, bent-tube boilers that operate at 85% efficiency, standard. The tangent tube design allows for unsurpassed convective internal pumping and maximum heat transfer.
Standard designs are available in both ASME Section I and IV. Unilux and Evolv boilers have the greatest size range of standard products available in this design and can be used wherever steam or hot water is required.
Key Considerations in Specifying Steam & Hot Water Boilers
Steam boilers are designed to meet different steam demands and typically fall into two categories:
- Low Pressure Steam Boilers – operating at or below 15 PSIG under Section IV of the ASME Boiler and Pressure Vessel Code
- High Pressure Steam Boilers – operating above 15 PSIG, regulated under Section I the ASME Boiler and Pressure Vessel Code
Low pressure steam boilers are commonly used in heating and small industrial applications, while high-pressure systems are critical for processes requiring intense steam output, such as manufacturing and power generation.
Hot water boilers are often preferred for heating applications where temperatures are more consistent and less extreme than steam-based systems. They also fall into two categories:
- Hot Water to 250° – covered under Section IV of the ASME Boiler and Pressure Vessel Code
- Hot Water exceeding 250° – covered under Section I of the ASME Boiler and Pressure Vessel Code
Other considerations include:
- Boiler Fuel Sources – Options include natural gas, propane, oil, biofuels, and electricity. The selection depends on fuel availability, cost, emissions regulations, and energy efficiency goals.
- Load Types – Systems can be designed for steady loads that are common in some manufacturing processes, or fluctuating loads such as heating in large commercial buildings or batch processes in manufacturing. Load type can impact the size and type of boiler required
- Regulatory Compliance – Today’s boilers must also meet stringent emissions requirements, particularly in terms of NOx and CO2 output
- Space Requirements – Facility space constraints often dictate whether compact boiler designs or larger, multi-unit systems are necessary
- Cost and Lead Time – Larger, more complex systems have longer lead times and higher initial costs, while simpler systems are more affordable and can be delivered faster
- Maintenance and Cost of Ownership – This includes overall efficiency of the boiler system, regular inspections, parts replacement, and emissions monitoring, which should be factored into the decision-making process.
No matter what type of boiler is selected, proper maintenance is crucial to extending its lifespan and ensuring operational efficiency.
Need a Stronger Boiler? Consider a High Pressure Steam Boiler
High-pressure steam boilers are important for industrial processes that need the higher temperatures associated with elevated steam pressures. These steam boilers are used in many utility and manufacturing applications to generate the steam required to power a variety of industrial processes.
High pressure steam boiler characteristics:
- Produce steam above 15 PSIG up to 800 PSIG
- Temperatures will exceed 250 degrees F up to 1200 degrees F.
- May include a superheater to heat steam above saturation temperature.
Due to the high pressures and temperatures at which these boilers operate, they need to be monitored to ensure efficient and safe operation.
Operators of high pressure boilers must:
- Inspect switches, valves, & safety devices regularly
- Watch for leaks or other issues
- Fix problems immediately to prevent further damage
- Maintain proper chemistry in the boiler to prevent corrosion and scale
- Process Load
- Applications
Process Load
While low pressure steam boilers are most commonly used to provide heat for buildings and facilities, high pressure steam boilers are designed to provide energy for a variety of processes.
- Low Pressure Steam Boilers → Heat for Facilities
- High Pressure Steam Boilers → Energy for Processes
High pressure steam loads are referred to as process loads and are classified as batch load or continuous load.
- Batch Loads – used to meet short-term demands and produce load swings on the boiler
- Continuous Load – provides for more even and constant demand
When selecting a high pressure steam boiler, it is important to consider the type of process load that is required for the application. For batch loads, instantaneous demand can be very large. It is essential to select a high pressure boiler with a design that can meet the fluctuating demand.
Applications
High pressure steam boilers are used to support a wide range of high pressure steam processes in markets such as:
- Food processing
- Manufacturing
- Hospitals
- Factories
Whatever the high pressure steam boiler application may be, the process should be optimized for efficiency. A high pressure steam boiler that is too large for the application can mean wasted energy. A well-qualified and highly experienced high pressure steam boiler supplier will be able to analyze the application and design an optimal system that meets process needs while maintaining energy efficiency.
Learn More About Steam Boilers
- Steam Pressure
- Applications
- Usage and Steam Load
- Fuel
- Controls
- Ancillary Equipment
Steam Pressure
Boilers normally operate at a pressure slightly higher than that which is needed so that line losses may be overcome as steam travels through the system. Generally, more steam (thermal energy) can be delivered to the heating equipment in higher-pressure steam using smaller diameter piping than in low-pressure systems. Sometimes high-pressure steam is delivered but the pressure is then reduced at the point of use via a pressure regulator or back-pressure steam turbine.
This highly efficient configuration is known as “Combined Heat and Power” or CHP and can be employed in larger steam systems where the boiler has the ability to generate steam at a much higher pressure than is needed for the process. In this concept, high-pressure steam is generated using low-cost natural gas and then is efficiently converted to electrical power via a backpressure steam turbine generator. The difference in pressure and the steam flow will determine how much power can be generated at the turbine generator. Typical minimums are 10,000 pph steam flow and 100 psig pressure deltas. As the cost of electrical power from the grid increases, the economic viability of these systems will continue to improve. Many industrial clients like the added reliability that onsite power generation brings to a facility.
Typically steam systems are categorized according to pressure requirements and pressure (and psi refers to psi-guage).
- 15 psi or less – limited area heating, humidification, low-temperature applications.
- 15 psi to 150 psi – larger facility heating needs, process applications
- Above 150 psi – industrial facility, large campus needs, or processes requiring fluctuating pressure levels
- Superheated steam – typically over 150 psi, and used in power generation, or to reduce condensate formation in long piping runs.
Applications
Steam boilers are used in a variety of applications, which require distinct pressures and flow rates. The steam boiler technology you select should be one that results in SAFE, efficient, and reliable operation.
Proper boiler sizing is also important, sometimes two smaller units sized for ½ of the peak load is a better choice than one large unit designed for peak loads, but normally operates inefficiently at a fraction of its maximum continuous rating.
-
Heating – Typically 150 psi or less
Heating applications in this range are usually food and beverage, processing factories, hospitals, and campus-type settings. Saturated steam may be used in process fluid heat exchangers, reactors, combustion air pre-heaters, and various other types of heat transfer equipment.
-
Humidification – Typically 150 psi or less
HVAC systems often include steam humidifiers to condition the air for indoor comfort and climate control. When the cold air is heated the relative humidity of the air drops, so it must be adjusted to normal levels with the addition of a controlled injection of dry saturated steam into the downstream air flow.
-
Process & Power – 150 -1000 psi with superheat
Higher-pressure steam boilers can provide very high temperatures needed for refining or chemical processes. Through the use of “step-down regulators” or back-pressure steam turbine generators, it is possible to supply steam at different pressures depending on the different needs of the various processes.
Usage and Steam Load
Understanding your usage and steam load is essential in selecting the right steam boiler for your application. Different steam boiler technologies perform better depending on the application profile. The primary difference lies in whether the usage profile is steady or fluctuating.
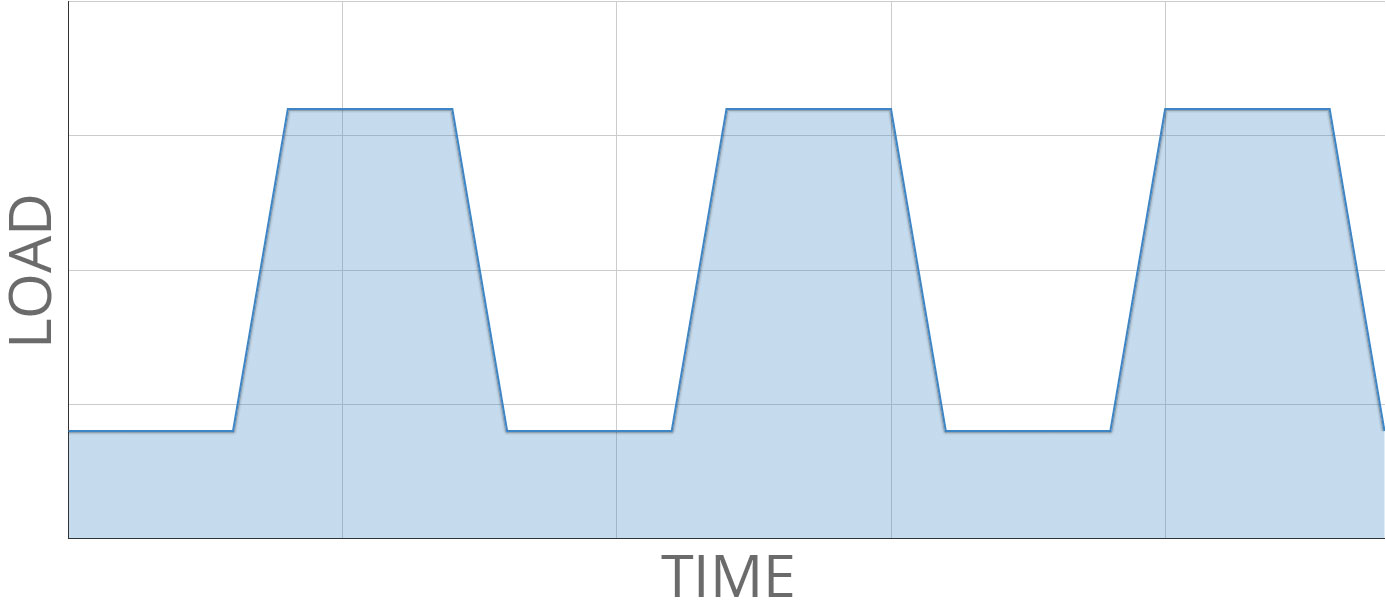
Steady Load
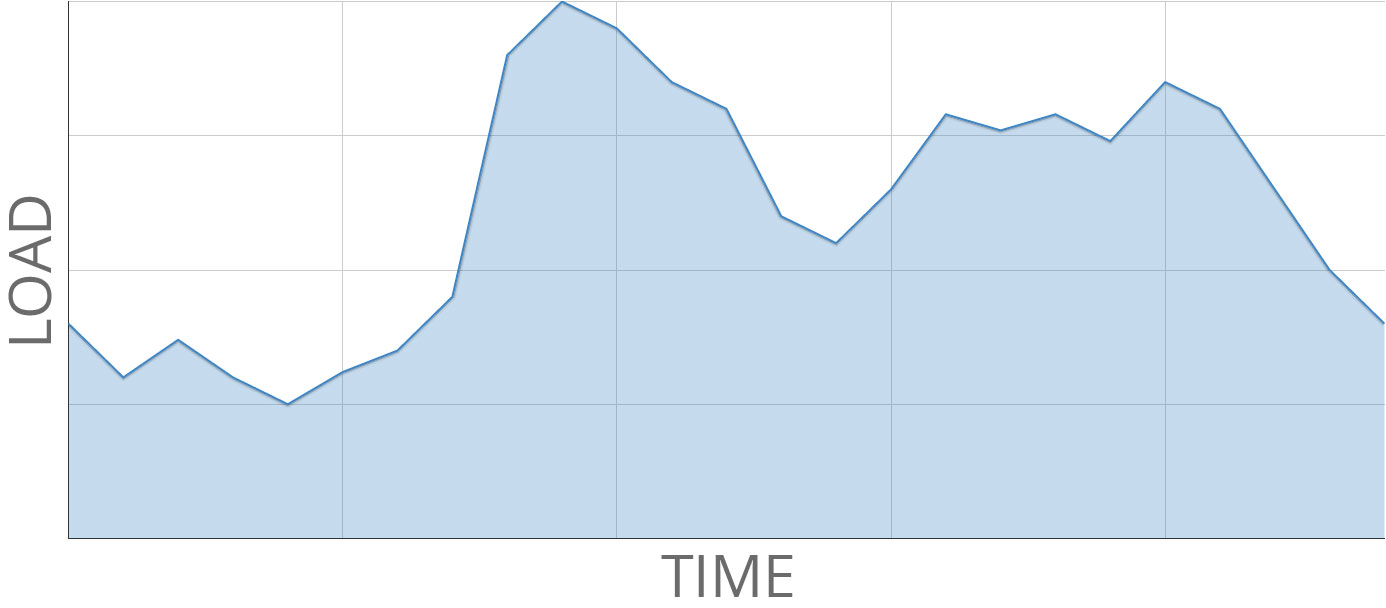
Fluctuating Load
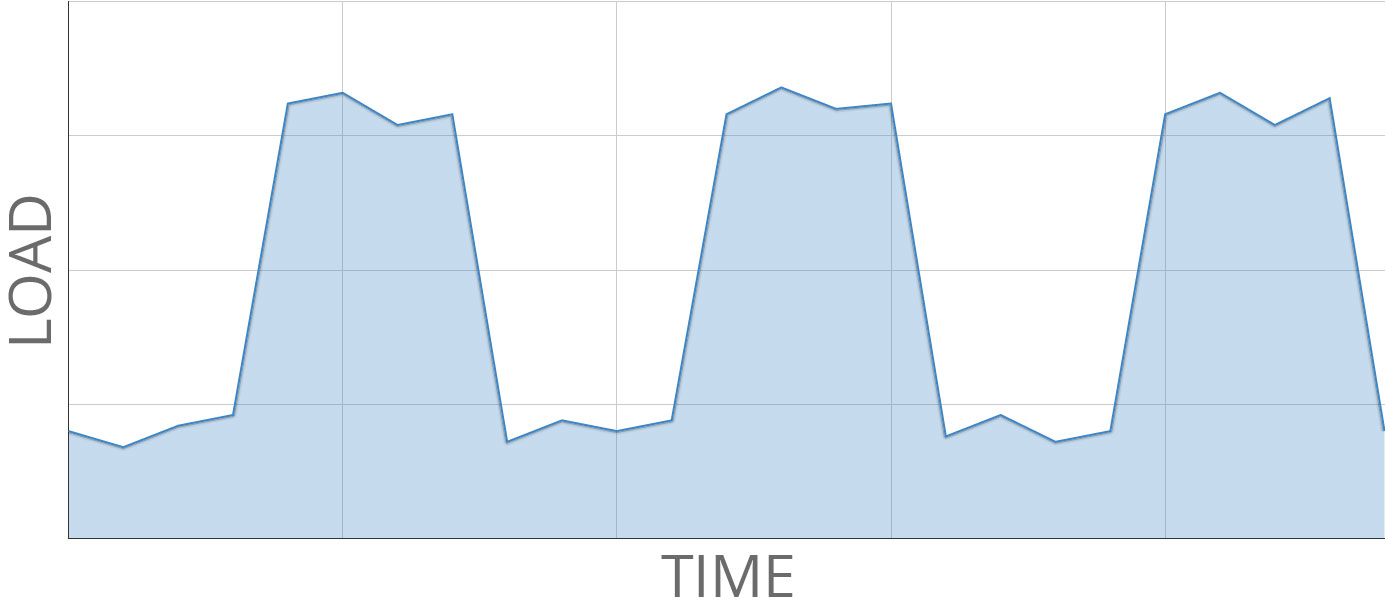
Combination Load
Fuel
Natural gas is the predominantly used fuel source for powering steam boilers because it is readily available, low cost, and clean burning. Other fuel sources include petroleum gas, propane, electricity, and alternative fuels. It is not uncommon to have a dual fuel burner that can fire both a primary fuel as well as a backup fuel.
A normal arrangement might be natural gas as a primary with secondary oil or propane as the backup in case of a gas line disruption. The standby fuel is normally stored onsite and is used only in emergencies. Critical care facilities, hospitals, prisons, and some industrial processes routinely use a backup fuel strategy and may store up to several days’ supply onsite.
Renewable fuels or “Opportunity Fuels” are receiving more attention these days with the increased focus on reducing overall plant emissions. Seldom are these fuels economically viable in smaller applications but can be worth considering in larger systems where there are multiple economic forces driving a decision. Boilers and the associated auxiliary systems needed for these fuels are generally more complex and expensive than standard gas-fired boilers.
Typical “opportunity fuels” include wood chips, digester gas, refuse-derived fuels, and various industrial or manufacturing by-products.
Controls
In their simplest form, steam boiler controls function to sense steam pressure and increase or decrease the burner firing rate as the steam pressure deviates from a prescribed set point pressure. Some control systems simply cycle the burner on or off as steam is needed. Boiler controls can range from these very basic on-off systems to the very sophisticated with precise and adaptive fuel and air matching, the cost and complexity of these systems vary accordingly.
Simple controls’ systems include the following:
- Burner management and boiler safety systems that monitor all boiler burner safety and provide shutdown and alarm functions when conditions are out of set limits.
- Proportional or on-off burner controls that increase or decrease fuel and air input to a boiler to match the heating loads of the facility.
- Boiler water level control via opening or closing a feedwater valve to maintain safe boiler water levels.
More advanced boiler controls are used on larger units where annual fuel costs warrant increased control of fuel and air. These systems normally include some or all of these features:
- Burner management systems are normally packaged by the burner manufacturer which are microprocessor or PLC-based and are integrated into the overall boiler controls system by the boiler manufacturer.
- These systems may also include single loop controllers to manage draft control, boiler blow-down functions as well as efficient fuel and air matching. Independent control of fuel and air valves via digitally controlled actuators with a feedback loop that minimizes excess oxygen in the boiler exhaust (above what is needed for full combustion) can significantly improve the annual boiler efficiency.
- Large industrial and campus heating plants often require remote monitoring or control, so more sophisticated boiler controls typically include some form of interface with the plant-wide supervisory control and data acquisition system. This may be any widely used communications protocol such as MODBUS, BACnet, LonWorks, or Ethernet.
Boiler and burner manufacturers have standardized on several systems recognized in the industry as being well-established and well-supported. However, using a manufacturer’s standard can be a two-edged sword. It is not uncommon to see boiler/burner controls over-specified to the point where even a capable operating staff is unable to troubleshoot the system or to make even simple changes without calling in outside tech support.
There are many standard systems available that offer flexibility and expansion capability that are well-known by many reputable boiler/burner service companies.
Ancillary Equipment
The steam boiler is part of a system, which requires ancillary equipment to function effectively. The right equipment and a properly designed system ensure that the boiler will function safely, reliably, and efficiently.
- Feedwater Tanks – used for the preheating of cold makeup water, collecting condensate return, and providing storage of water to steam-generating boilers.
- Deaerators – used for the removal of oxygen and other dissolved gases from the feedwater to steam-generating boilers
- Condensate Surge Tanks and Heat Recovery – for the collection of condensate returns, which contain valuable water treatment chemicals and thermal energy
- Blowdown Separators and Heat Recovery – used to take water from the boiler during blowdown and reduce it to atmospheric pressure for disposal
- Economizers – heat exchange devices used with a boiler to preserve energy by using the exhaust from the boiler to recapture steam or preheat the cold water used to feed the boiler. Some of the types of economizers are stack, flash, and condensing heat recovery.
Learn More About Hot Water Boilers
- Applications
- Usage and Hot Water Load
- Fuel
- Controls
- Required Water Temperatures
- Condensing vs Non-Condensing Temperatures
Applications
Hot water boilers are used in applications that require specific water temperature requirements. The hot water boiler technology you select should be one that results in safe, efficient, cost-effective, and reliable operation. It is important to choose a hot water boiler that is designed to meet your applications in order to achieve optimal efficiency.
-
Comfort Heating – Typically 100° – 200°F
Heating applications in this range are usually building heating for commercial buildings, office buildings, hospitals, etc. Depending on the system design and the associated air handling equipment, a condensing boiler may be able to be used to achieve higher efficiency as low water temperatures may be able to be utilized. -
Domestic – Typically 100° – 160°F
Domestic hot water boilers are similar to comforting heating boilers but have a slightly different design for domestic use. They typically operate at lower water temperatures. -
Process (Continuous & Batch) – Typically 160° – 200°F
Heating applications in this range are usually food and beverage, chemical facilities, and processing-type factories. They typically require standard temperature boilers due to the process requirements. -
District Heating – Typically 200° – 500°F
High-temperature hot water boilers can provide very high temperatures needed for distributing heat throughout a campus loop. These could be utilized at institutional-type facilities (hospitals, universities, etc.) or a large corporation with a campus-style setup.
Hot water boilers can be advantageous because they normally do not need an operator or special water chemistry, and they run at higher fuel conversion efficiency than steam boilers.
Usage and Hot Water Load
Understanding your minimum and maximum usage and hot water load profile is essential in selecting the right boiler for your application. Different hot water boiler technologies perform better depending on the application profile. The primary difference lies in whether the usage profile is steady or fluctuating.
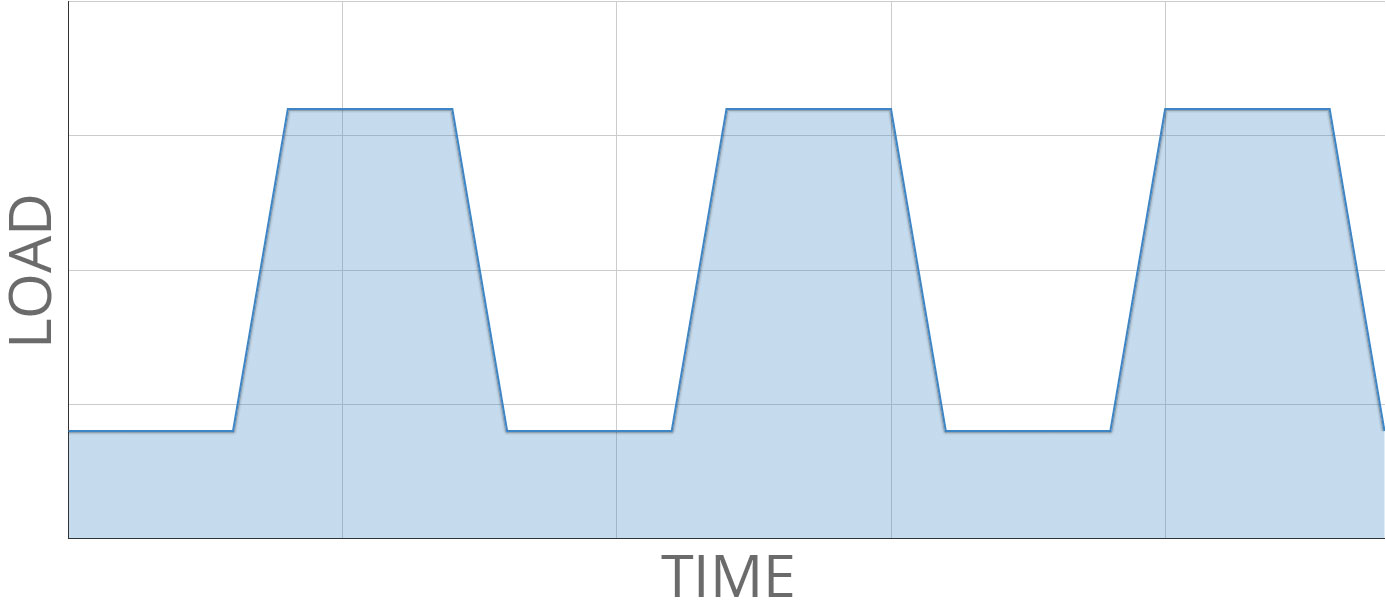
Steady Load
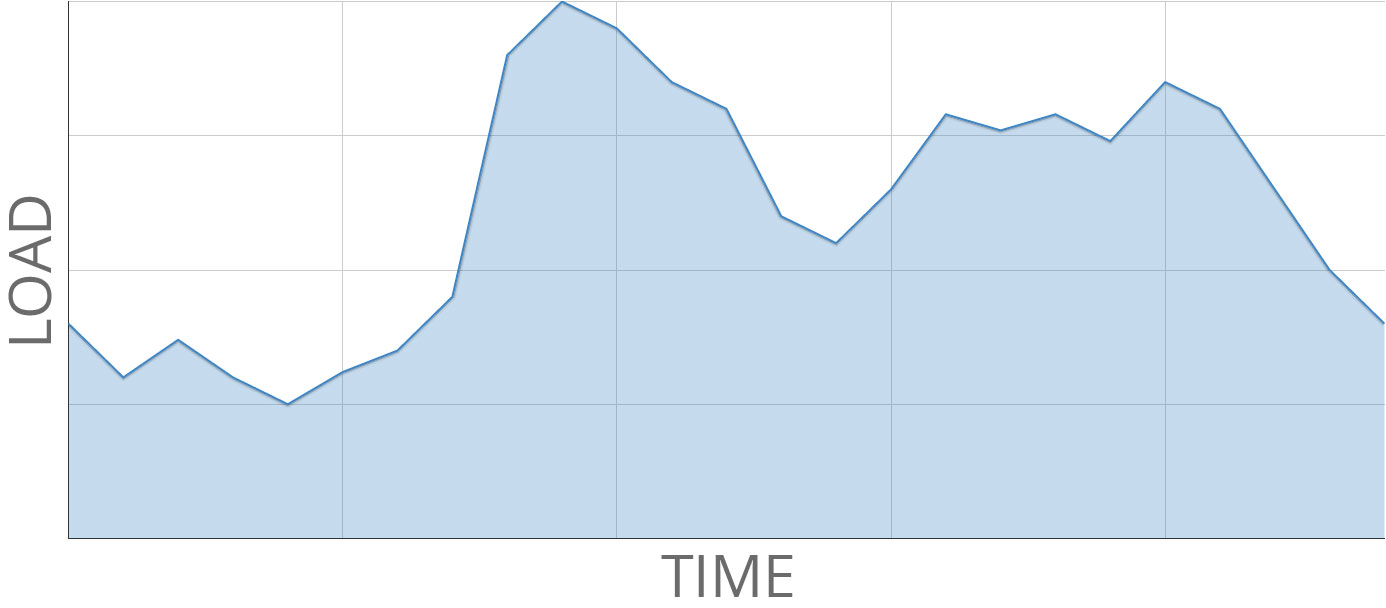
Fluctuating Load
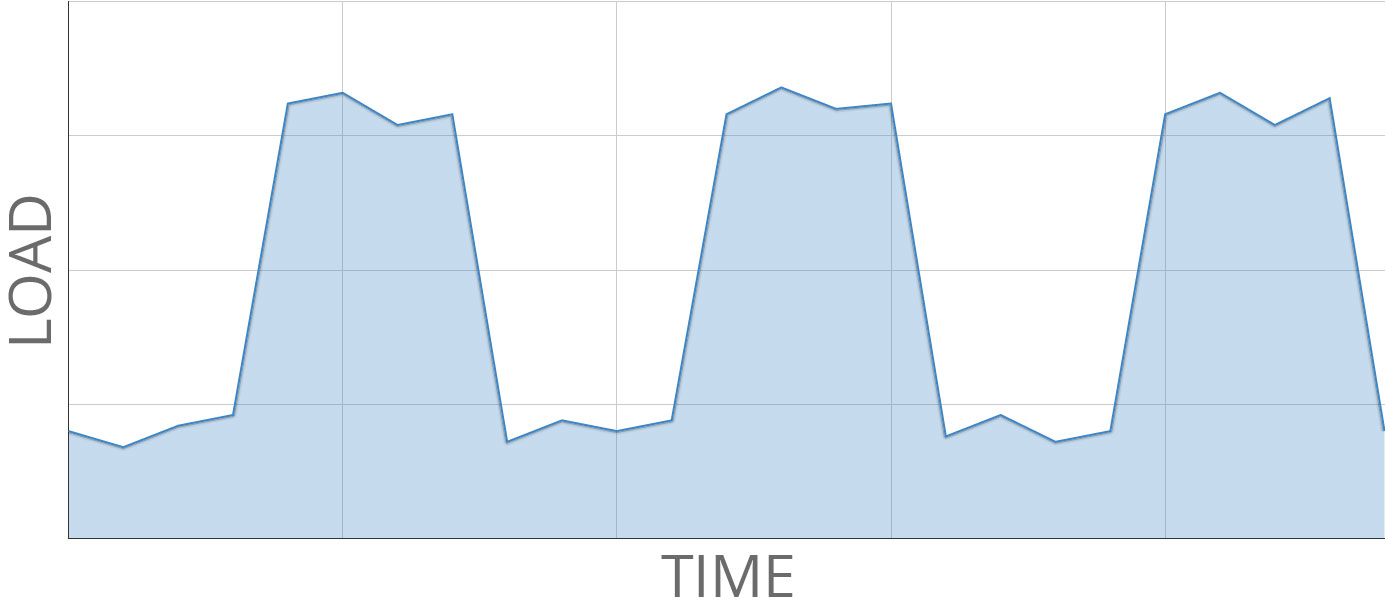
Combination Load
Fuel
Natural gas is the predominantly used fuel source for powering steam boilers because it is readily available, low-cost, and clean-burning. Other fuel sources include:
- Petroleum gas
- Propane
- Electricity
- Alternative fuels
It is possible to have a dual fuel burner that can fire both a primary fuel and a backup fuel. A normal arrangement might be natural gas as a primary with a secondary oil or propane as the backup, in case of a gas line disruption. The standby fuel is normally stored onsite and is used only in emergencies. Critical care facilities, hospitals, prisons, and some industrial processes routinely use a backup fuel strategy and may store up to several days’ supply onsite.
Renewable Fuels
Renewable fuels or “opportunity fuels” are receiving more attention with today’s increased focus on protecting the environment. These include:
- Wood chips
- Digester gas
- Refuse-derived fuels
- Various industrial or manufacturing by-products
Seldom are these fuels economically viable in smaller applications but can be worth considering in larger systems where there are multiple economic forces driving a decision. Boilers and the associated auxiliary systems needed for these fuels are generally more complex and expensive than standard gas-fired boilers.
Controls
Steam boiler controls function to sense water temperatures and increase or decrease the burner firing rate as the water temperature deviates from a prescribed set point pressure. Some control systems simply cycle the burner on or off as hot water is needed. Boiler controls can range from these very basic on-off systems to very sophisticated, with precise and adaptive fuel and air matching. The cost and complexity of these systems vary. Our team can assist you in evaluating and choosing the best system for your needs.
Simple controls systems include the following:
Burner management and boiler safety systems – monitor all boiler burner safety; provide shutdown and alarm functions when conditions are out of set limits.
Proportional or on-off burner controls – increase or decrease fuel and air input in a boiler to match the heating loads of the facility.
Boiler water level control – via opening or closing a feedwater valve to maintain safe boiler water levels.
More advanced boiler controls are used on larger units where annual fuel costs warrant increased control of fuel and air. These systems may include the features below:
Burner management systems – normally packaged by the burner manufacturer, microprocessor, or PLC-based and -integrated into the overall boiler controls system by the boiler manufacturer.
Single loop controllers – to manage draft control, boiler blowdown functions as well as efficient fuel and air matching. Independent control of fuel and air valves, via digitally controlled actuators, with a feedback loop that minimizes excess oxygen in the boiler exhaust (above what is needed for full combustion), can significantly improve the annual boiler efficiency.
Remote monitoring or control – often required by large industrial and campus heating plants have more sophisticated boiler controls that usually include some form of interface with the plant-wide supervisory control and data acquisition system.
Required Water Temperatures
When selecting a hot water boiler, it is important to consider the required water temperature for both the supply and return water.
- Supply water temperature – refers to the temperature of the water as it leaves the boiler and travels to your heating or process system and equipment.
- Return water temperature – refers to the water as it returns to the boiler, which will be the more crucial factor in your boiler selection.
Condensing vs Non-Condensing Temperatures
In choosing between a condensing and a non-condensing hot water boiler, the return water temperature is the determining factor. Condensing boilers are designed to achieve high efficiency by condensing water vapor in exhaust gases and recovering the latent heat, which would otherwise be wasted.
Unless the return water temperature is 140° or below, your application may not benefit from the use of a condensing boiler. Condensing boilers are most often a good choice for low-temperature applications, because of the possibility of higher efficiencies.
The basic temperature options with hot water boilers include:
- Low-temperature (100° – 150°F)
- Standard temperature (150° – 240°F)
- High temperature (240° – 500°F)